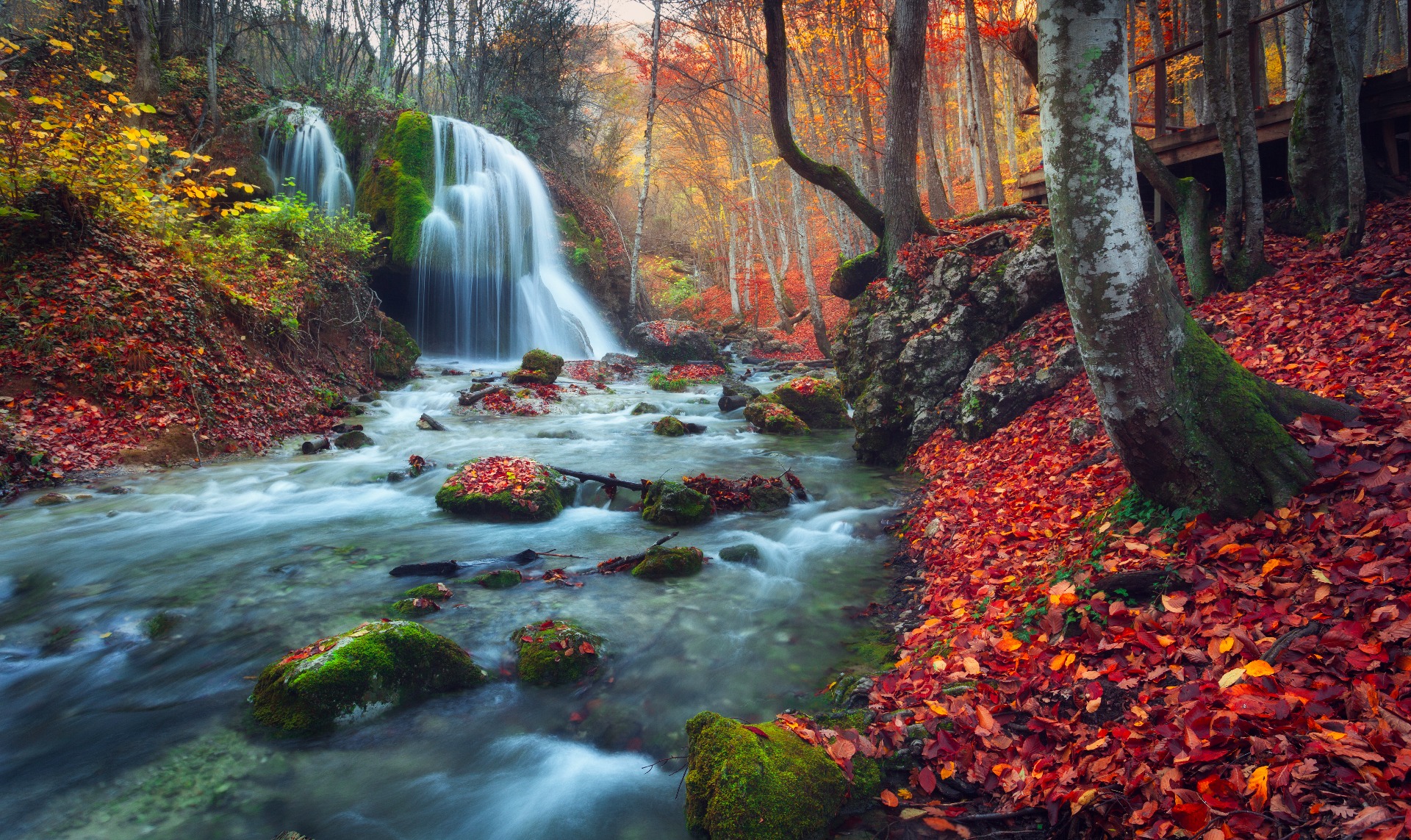
Підготовка до практичних занять
Матеріал до занять
з дисципліни ОКМ та ТВКМ для студентів гр.Т-41
ТЕМА : Загальні відомості про виробництво чавуну та сталі
Поняття про металургію. Характеристика металургійних процесів.
Галузь промисловості, що займається виробництвом металів і сплаві з руди та іншої сировини, наука про способи одержання та очистки металів називається металургією.
Спочатку залізо одержували безпосередньо із руди відновленням в горнах. Внаслідок насичення заліза вуглецем, одержували сплав крихкий, але з гарними ливарними якостями. Цей сплав назвали чавуном. Потім чавун почали переробляти в сталь - сплав з меншим, ніж у чавуні, вмістом вуглецю, марганцю, кремнію та ін., що володіє високою пластичністю і міцністю. Двохстадійна схема виробництва сталі - виплавка чавуну в доменній печі і переробка його в сталь - є і сьогодні основною.
Характеристика матеріалів, що застосовуються в металургії. Для виробництва металів використовують руди, флюси, паливо і вогнетривкі матеріали.
Руда - це гірські породи, що містять метали в кількостях, що забезпечують їх економну переробку. Скажімо, залізні руди містять 30...60 % металу. Руда складається із мінералів, що містять метал у вигляді окислів, сульфідів, карбонатів і пустої породи, до складу якої входить кремнезем SiO2 , глинозем Al2O3 , а також домішки сірки, фосфору, миш'яку та ін.
Флюси - це матеріали, що утворюють при плавці шлак - легкоплавку сполуку з пустою породою руди, золою палива і іншими неметалічними включеннями. Звичайно шлак володіє меншою густиною, ніж виплавляємий метал, тому він розташовується над ним, захищаючи його від взаємодії з пічними газами і повітрям.
Паливом в металургійних процесах служить кокс, природний, доменний коксовий газ, мазут.
Кокс одержують сухою перегонкою кам'яного вугілля без доступу повітря при температурі 1000...1100 ºС. Він містить 85...90 % С, має високу питому теплоту згоряння, малу зольність.
Природний газ - висококалорійне дешеве паливо і складається в основному із метану СН4.
Доменний газ - побічний продукт при виплавці чавуну в доменній печі (містить до 32 % СО, до 4 % Н2).
Мазут - важкий залишок перегонки нафти, містить до 88 % С, 10...12 % Н2 і невелику кількість кисню та сірки.
Вогнетривкі матеріали застосовують для внутрішнього облицювання (футерівки) плавильних печей і іншого обладнання, що знаходиться під дією високих температур і розплавлених металів і шлаків. Це динасова цегла, кварцовий порошок, шамот, хромомагнезит та ін.
Поняття про металургію чавуна. Характеристика залізних руд і підготовка їх до плавки. На сучасному етапі до 85 % чавуну витрачається на виробництво сталі.
Сировиною для виплавки чавуну служать залізні руди, флюси і паливо. Залізо в рудах в основному знаходить у вигляді окислів, рідше у вигляді карбонату FeCO3. Серед залізних руд використовується магнітний залізняк, що містить до 65 % заліза у вигляді магнітного окислу Fe3O4 (магнетит), червоний залізняк, що містить до 60 % заліза у вигляді безводного окислу Fe2O3 (гематит), бурий залізняк, що містить до 50 % заліза у вигляді гідроокису 2Fe2O3·3Н2О (лимоніт) та Fe2O3·Н2О (гетит) - це бідні руди забруднені миш'яком та фосфором, шпатовий залізняк - бідна руда, що містить до 40 % заліза у вигляді карбонату FeCO3 (сидерит), містить небагато сірки та фосфору.
Основна маса руди (приблизно 95 %) проходить стацію попередньої підготовки до плавки, що включає в себе подрібнення, сортування, збагачення та кускування. Спочатку руду подрібнюють, а потім сортують. Придатними для плавки вважаються шматки (куски) розміром 40...100 мм. Більше 80 % всіх руд піддають збагаченню, шляхом магнітної сепарації. Попереднім випалюванням руди при температурі 600...800 ºС немагнітні окисли переводять у магнітні.
Паливо в процесі виплавки чавуну в доменній печі виконує роль не тільки пального, але й відновлювачем заліза з руди.
Флюсами при виплавці чавуну в доменній печі служать вапняк СаСО3 або вапняк, що складається з СаСО3 та MgСО3.
Будова і робота доменної печі та допоміжного устаткування.Чавун із залізної руди виплавляють в домнах - вертикальних печах шахтного типу.
Для виплавки чавуну в домну завантажують шихту - суміш певного співвідношення руди, палива і флюсів. Окремі порції шихти називаються колошами. Колоші з бункера (слайд 2.1-1, плакат) подаються вагонетками у приймальну воронку засипного апарату. Шихта попадає по черзі в колошник і далі в шахту печі. Шихта завантажується в домну періодично (бо домна відноситься до печей безперервної дії протягом 5...10 років) по мірі згоряння палива і випуску чавуну і шлаку.
Найширша циліндрична частина домни називається розпаром. Нижче нього знаходяться звужувальні заплечики і горн, обмежений лещаддю. В нижній частині горна розташовані ливники для випуску чавуну і шлаку.
Для підтримання горіння палива в домену піч через ряд розташованих по колу фурм вдувається під тиском до 0,25 МПа повітря. Витрати повітря на виплавку 1 т чавуну становить 3000...7000 м3/хв.
Основними характеристиками доменної печі служать її корисна висота (відстань від лещаді до нижнього конуса засипного апарату) і корисний об'єм (робочий об'єм, заповнений шихтою і продуктами плавки). Сучасні домені печі мають: корисний об'єм 2000...5000 м3, добову продуктивність 3000...10000 т, корисну висоту до 35 м.
Фізико - хімічні процеси, що відбуваються в доменній печі. Демена піч працює по принципу протитоку: шихтові матеріали рухаються зверху вниз, а назустріч їм піднімається потік гарячих газів - продуктів згоряння палива. При цьому відбуваються наступні процеси: горіння палива, відновлювання та збагачення заліза вуглецем ("науглераживание"), відновлення інших елементів, утворення шлаку.
При температурі 750...900 ºС в шихті відновлюється залізо:
3Fe2O3+СО = 2Fe3O4+СО2; Fe3O4+СО = 3FeO+СО2; FeO+СО = Fe+СО2.
В результаті цих реакцій утворюється тверде губчасте залізо. При температурі 1000...1100 ºС губчасте залізо збагачується вуглецем:
3Fe+2CO = Fe3С+СО2; 3Fe+C = Fe3С.
Вуглець знижує температуру плавлення залізовуглецевого сплаву, тому, опускаючись в нижню частину шахти, сплав починає плавитися додатково насичується вуглецем та іншими елементами, відновленими з руди - марганцем, кремнієм, фосфором, сіркою.
Таким чином, в результаті відновлення заліза, марганцю, кремнію, фосфору та сірки і їх розчиненні в залізі в горні печі утворюється чавун. Разом з чавуном в нижній частині печі збирається шлак - сплав пустої породи, флюсів, золи палива, а також частина невідновлених окислів.
В процесі утворення і накопичення чавун і шлак по різним ливникам випускають із печі: чавун - через 3...4 год., а шлак - через 1,0...1,5 год.
Інтенсифікація доменного процесу. Для інтенсифікації процесу плавки і більш економної витрати палива повітря, що вдувається, попередньо нагрівають до 1000...1200 ºС у повітронагрівачах (кауперах).
Поняття про виробництво сталі із чавуну.Сталь відрізняється від чавуну меншим вмістом вуглецю, кремнію, марганцю, домішок сірки та фосфору. Основною сировиною для виробництва сталі є передільний чавун та стальний металобрухт. Передільний чавун, як правило, містить 3,8...4,4 % С, 0,2...2,0 % Si, 0,6...3,5 % Mn, 0,07...1,6 % P, 0,03...0,08 S. Суть переробки чавуну в сталь полягає у зменшенні в ньому вмісту вуглецю та інших елементів і переводу їх у шлак або гази. То ж сталь одержують окисленням надлишку С, Si, Mn, S та P.
На сучасному етапі сталь одержують в кисневих конвертерах, мартенівських та електричних печах.
Характеристика конвертерного способу виробництва сталі.Суть киснево-конвертерного процесу полягає у продуванні рідкого чавуну киснем. Кисневий конвертер представляє собою посудину грушовидної форми із стального листа, внутрішня частина якого футерована основними вогнетривкими матеріалами (слайд 2.1-2, плакат). Робоче положення конвертера - вертикальне. Кисень подається в нього під тиском 0,8...1,0 МПа за допомогою водоохолоджуваної фурми, що введене в конвертер через горловину і розташована над рівнем рідкого металу на відстані 0,3...0,8 м.
Перед початком роботи конвертер завантажують до 30 % стального брухту, потім заливають рідкий чавун при температурі 1250...1400 ºС, вводять кисневу фурму, подають кисень і додають шлакоутворюючі матеріали.
В момент, коли вміст вуглецю досягає заданого для даної марки сталі, подачу кисню припиняють, конвертер повертають і виливають спочатку сталь, а потім - шлак. Продуктивність кисневого конвертера ємністю 300 т досягає 400...500 т/год, в той час як продуктивність мартенівських і електропечей не перевищує 80 т/год.
Характеристика мартенівського способу виробництва сталі. Матеріалами для виплавки сталі в мартенівській печі можуть бути: стальний брухт, рідкий і твердий чавуни, залізна руда. Флюсом служить вапняк СаСО3 (8...12 % від маси металу). Спочатку в піч завантажують і прогрівають залізну руду і вапняк, потім додають стальний брухт (скрап) і заливають рідкий чавун. Для інтенсифікації процесу плавлення і окисленні домішок ванну продувають киснем. Продувка киснем дозволяє скоротити тривалість процесу у 2...3 рази, зменшити витрати палива і залізної руди.
Характеристика способу виробництва сталі в електропечах.Порівняно з іншими плавильними агрегатами електропечі володіють рядом переваг: здатністю швидкого нагрівання і підтримання заданої температури в межах 2000 ºС, можливістю створення окислювальної, відновлювальної та нейтральної атмосфери, а також вакууму. Це дозволяє виплавляти в електропечах сталі і інші сплави з мінімальною кількість шкідливих домішок та сталі зі спеціальними властивостями. Металургійні печі поділяють на дугові і індукційні.
У дуговій електропечі джерелом тепла є електрична дуга, що виникає між електродами діаметром 350...550 мм і шихтою при подачі на електроди напруги 200...600 В і струму 1...10 кА. Плавка з окисленням схожа з мартенівським процесом. Плавка без окислення застосовується для одержання легованих сталей.
Індукційні печі порівняно з дуговими мають ряд переваг:
- відсутність дуги дозволяє виплавляти метали з малим вмістом вуглецю і газів; - виникаючі електродинамічні сили перемішують рідкий метал, вирівнюючи хімічний склад і умови спливання неметалічних включень;
- ці печі маю невеликі розміри, що дозволяю розміщувати їх в спеціальних камерах, створюючи будь-яку атмосферу чи вакуум.
В цих печах плавку звичайно проводять методом переплавки легованих сталей або чистого по сірці та фосфору вуглецевого скрапу і феросплавів.
Тривалість плавки в індукційній печі ємністю 1 т складає 45 хв., витрати електроенергії на 1 т сталі - 600...700 кВт·год.
Поняття про розливання сталі. Характеристика видів розливання сталі. Виплавлену в плавильній печі сталь випускають у сталерозливний ківш і мостовим краном переносять до місця розливання злитки. Сталь розливають у виливниці ("изложницы") або кристалізатори установок для безперервного розливання.
Виливниця представляє собою чавуну форму для одержання злитків різного перерізу (слайд 2.1-3, плакат). Маса злитків для прокату становить 10...12 т, а для поковок досягає 250...300 т. Застосовують два способи розливання сталі у виливниці: зверху і сифоном. Розливання сифоном здійснюється у виливниці внизу вверх одночасно у 2...60 встановлених на піддоні виливниць через центровий літник і канали у піддоні. При цьому забезпечується плавне, без розбризкування їх заповнення; поверхня злитка - чиста, скорочується час розливання.
Пряме відновлення заліза з руди. Заслуговує на увагу розробка процесу прямого відновлення заліза з руди. Виключення із виробництва сталі проміжного процесу - одержання чавуну - економічно вигідне. Задача складна.
Найбільш розповсюдженим є виробництво губчастого заліза. Це пористий напівпродукт (95 % заліза, 5 % оксидів заліза, 0,01...0,016 % S і 0,01 Р, домішок породи та ін.), що виплавляється у сталеплавильних агрегатах, у сталь. Відновлення шихти ведеться у невеликих за висотою шахтних печах у суміші газів СО+Н2. Як і у доменних печах, процес заснований на принципі протитоку: залізорудні матеріали завантажують зверху, а відновлювальні, нагріті приблизно до 1200 ºС, гази поступають знизу. В зоні відновлення температура становить 850...900 ºС.
Поняття про способи одержання високоякісної сталі.Для одержаннявисокоякісної сталі застосовують методи спеціального переплавлення, що покращують структуру сталі і її властивості. До таких методів можна віднести переплав у вакуумній індукційній печі (одержується сталь чиста по газам, сірці та фосфору), у вакуумній дуговій печі , електрошлаковий переплав, позапічна обробка тощо.
Основи технології ливарного виробництва та обробки металів тиском. Поняття про порошкову металургію. Основні види порошкових матеріалів.
Для одержання заготовок деталей найважливіша роль належить ливарному виробництву.
Способи виготовлення відливок. Класифікація та характеристика різновидностей ливарних форм.
Виробництво брикетів здійснюють найбільш розповсюдженими методами: холодним та гарячим пресуванням.
Методом порошкової металургії одержують компактну металокераміку, металокерамічні тверді сплави, антифрикційні і фрикційні вироби, порошкові фільтри тощо.
Завдання для самостійного опрацювання з дисципліни "Технологічний практикум"
Класифікація металорізальних верстатів та їх будова
Металорізальними верстатами називають машини для формування деталей із металів шляхом зняття стружки або без зняття стружки (обкатування роликами, нанесення рифлень і ін.). Будь-який верстат, як і всяка машина, складається із трьох основних механізмів: рушійного, передавального і виконавчого. Виконавчий механізм одержує рух від рушійного через передавальний і забезпечує відносне переміщення заготовки і інструменту, чим і визначається формування деталі. Передавальний механізм представляє собою сукупність пристроїв, що передають рух від двигуна до виконавчих органів верстату (шпинделю, супорту, столу), він називається приводом верстата.
Металорізальні верстати поділяють на групи відповідно до методів обробки різанням: точіння, фрезерування, свердлення, стругання, протягування.
Характеристика металорізального інструменту.Основними інструментами для токарних верстатів являються різці різних типів, а також свердла, зенкери, розвертки, мітчики, плашки і ін.
Різець складається із робочої частини або головки і стержня або тіла, призначеного для кріплення різця у різцетримачеві (таблиця). На робочій частині різця заточуванням утворюються поверхні: передня і задня. Перетин передньої і задньої поверхонь утворюють різальні кромки - головну і допоміжну. Сполучення головної і допоміжної різальних кромок утворюють вершину різця.
Кути різальної частини різця, що визначають його геометричну форму, суттєво впливають на процес різання. Оптимальні значення кутів різців і іншого різального інструменту для обробки різних матеріалів залежать від його характеру, матеріалу інструмента, розмірів і форми деталей тощо.
Технологія обробки металів на верстатах. Технологія роботи на металорізальному верстаті визначається методом обробки та видом операцій, формою і розмірами деталі та ін.
При обробці циліндричних поверхонь застосовують повздовжнє переміщення супорту. Зовнішні циліндричні поверхні обробляються звичайними прохідними різцями, внутрішні - розточувальними. Для одержання отвору у суцільному матеріалі, його спочатку просвердлюють. Свердління, зенкування і розвертування виконують відповідними інструментами, які встановлюють і пінолі задньої бабки.
Певну специфіку мають процеси обробки конічних і фасонних поверхонь, нарізання різьб тощо.
Поняття про електрофізичні та електрохімічні методи обробки матеріалів. В сучасному машинобудуванні з використанням спеціальних видів матеріалів обробка їх механічними методами вкрай утруднена. Для обробки важкооброблювальних матеріалів і складної форми з успіхом використовують електрохімічні та електрофізичні методи розмірної обробки. До них належать електроерозійні, електрохімічні, ультразвукові та променеві способи обробки.
В цих методах використовується перетворення електричної енергії електричних розрядів у теплову енергію.
Переваги цих методів перед іншими в тому, що:
1) цими методами можна обробляти будь-які матеріали, які володіють високими фізико-механічними властивостями;
2) завдяки простоті кінематики формоутворення можна вести обробку досить складних форм (глухі фасонні отвори, отвори дуже малих діаметрів та ін.);
3) можливість відображення форми інструмента по всій оброблюваній поверхні заготовки при простому переміщенні інструмента;
4) при обробці практично відсутній силовий вплив на заготовку;
5) обробку цими методами легко автоматизувати.
Заслуговує на увагу електроіскровий метод, який заснований на руйнуванні металу в колі постійного струму під дією іскрового розряду. Цим способом обробляють твердосплавні філь'єри, штампів, прес-форм тощо.
Завдання для самостійного опрацювання
період травень-червень 2022 року
Поняття про зварювання металів та його значення в народному господарстві.
Зварюванням металів називають процес одержання нероз'ємних з'єднань металевих виробів за рахунок використання міжмолекулярних та міжатомних сил зчеплення. Для приведення цих сил в дію необхідно зблизити атоми з'єднуваних металів на відстань порядку 10-8 см, тобто на відстань приблизно рівну параметру кришталевої гратки цих металів. Вказаному процесу зближення атомів і молекул сприяє нагрівання зварюваних поверхонь до розплавлення або пластичного стану і прикладення механічного зусилля стискування.
У теперішній час зварювання металів, як і обробка металів тиском, різанням або литтям, являється основним технологічним процесом виготовлення різних металевих конструкцій та виробів і знаходить широке використання у всіх галузях народного господарства, зокрема, у суднобудуванні. Особливо значний економічний ефект дає застосування зварювання при виготовленні важких зварювально-литих та зварювально-кованих конструкцій, використанні зносостійкої наплавки у виробництві валків прокатних станів, ковальсько-пресового обладнання, металорізального інструменту тощо.
Класифікація видів зварювання в залежності від виду енергії, що використовується, та зварних з'єднань. Сучасні способи зварювання класифікують за двома основними ознаками: за станом металу в процесі зварювання та за видом енергії, яка використовується для нагрівання зварюваних металів. За першою ознакою розрізняють зварювання плавленням і зварювання тиском.
При зварюванні плавленням кромки з'єднуваних деталей (основний метал) і в більшості випадків додатковий (присадний) нагрівають до розплавленого стану, утворюючи загальну зварювальну ванну. Після видалення джерела нагрівання метал ванни охолоджується і твердне, утворюючи зварний шов, що з'єднує зварювальні поверхні в одне ціле.
При зварюванні тиском зварювальне з'єднання утворюється нагріванням зварюваних поверхонь до пластичного стану або до початку плавлення і додатковим прикладанням механічних зусиль стискання. Такі пластичні метали, як мідь, свинець, алюміній, нікель і ін. Можна зварювати і в холодному стані за рахунок тільки тиску.
За видом енергії, що використовується для нагрівання металу, всі способи зварювання можна розділити на основні групи: електричні, хімічні, механічні і променеві.
Найбільш важливою являється група електричних способів, при яких метал нагрівається за рахунок електричної енергії. До цієї групи належать наступні види зварювання: дугова, контактна, електрошлакова, індукційна, плазмова.
До групи хімічних способів зварювання належать газова і термітна. Нагрівання металу при цих способах зварювання здійснюється за рахунок екзотермічних реакцій окислення різних речовин, що знаходяться у газоподібному або твердому стані.
До механічних способів зварювання відносяться: горнова або ковальська, холодна тиском, тертям, вибухом і ультразвуком. При цих методах зварювання для з'єднання металів використовують відповідні види механічної енергії.
Група променевих способів зварювання об'єднує електронно-променеве, лазерне та геліозварювання.
Із перерахованих способів зварювання найбільш важливе значення мають електродугове, контактне та газове.
Поняття про дугове електрозварювання. Властивості електричної дуги.Електричне дугове зварювання вперше було запропоноване нашим співвітчизником М.М. Бенардосом у 1882 р., який використав дугу для зварювання металів вугільним електродом, а у 1888 р. М.Г. Славянов запропонував спосіб дугового зварювання металевим електродом.
Зварювальна дуга представляє собою потужний електричний розряд в газах, що супроводжується виділенням значної кількості тепла і світла. Для розігріву катода між ним і анодом, підключеними до джерела зварювального струму, здійснюють короткочасне коротке замикання. Після відриву електрода від виробу з розігрітого катоду під дією електричного поля починається електронна емісія. При русі електронів до аноду вони стикаються з молекулами і атомами повітря і іонізують їх. На поверхні анода і катода відбувається нейтралізація заряджених частинок, що приводить до перетворення електричної енергії в теплову.
До основних параметрів, що характеризують електричну дугу, відносяться напруга, струм і довжина дуги. Зварювальна дуга складається із трьох частин: катодної, анодної і стоба дуги. Майже весь простір займає стовп дуги, в якому відбуваються процеси іонізації і переміщення заряджених частинок до катоду і аноду. Температура стовпа дуги досягає 6000...7000 оС. Він оточений ореолом, який представляє собою розпечену суміш парів електродного і зварювального металів та продуктів реакції цих парів з оточуючим газовим середовищем.
Для дугового зварювання застосовують як постійний, так і змінний струм. Джерелами постійного струму є зварювальні генератори постійного струму та зварювальні випрямлячі. При зварюванні змінним струмом використовують зварювальні трансформатори.
Величина напруги для запалювання дуги (напруга холостого ходу) повинна бути не нижче 30...35 В (при постійному струмі) і 50...55 В (при змінному струмі). Для стійкого горіння відкритої дуги в більшості випадків достатньо напруги 18...30 В.
Поняття про контактне електрозварювання. Характеристика видів електроконтактного зварювання. Контактне зварювання (зварювання опором) засноване на розігріві зварювальних виробів джоулевим теплом і механічним притискуванням розігрітих виробів. Згідно із законом Джоуля-Ленца кількість тепла, що виділяється при проходженні електричного струму у зварюваних деталях та перехідних контактах :
Q = kI2Rt (Дж).
Величина зварювального струму при контактному зварюванні досягає десятків і навіть сотень тисяч ампер. Такі струми одержують у знижувальних однофазних зварювальних трансформаторах, що мають у вторинній обмотці частіше за все один виток. Для регулювання зварювального струму первину обмотку роблять секційною. Опір місця зварювання залежить від чистоти і стану поверхні зварюваного металу. До основних видів контактного зварювання відносяться: стикова, точкова і шовна.
При стиковому зварюванні зварювані деталі (стержні, стрічки, рейки, труби) закріплюють в мідних затискачах машини. Переміщення рухомої плити і стискання зварюваних виробів здійснюють механізмом стиснення.
Точкове зварювання застосовують для з'єднання листових конструкцій, де необхідно забезпечити потрібну міцність, а щільність не є обов'язковою. Складені внахлест деталі затискають з певним зусиллям між мідними електродами, до яких підводиться струм від зварювального трансформатора. Тривалість витримки на жорстких режимах зварювання становить 0,001...0,1 с, густина струму - 150...350 А/мм2 і тиск на електроди - 40...100 МПа.
Шовне або роликове зварювання застосовують для одержання міцних і щільних швів при виготовленні тонкостінних посудин та тонкостінних труб. При шовному зварюванні збирають внахлест деталі, а потім затискають з певним зусиллям між двома мідними роликами, до яких підводиться струм від зварювального трансформатора. Одному з роликів надають примусового обертання від спеціального привода. При включенні струму і одночасному обертанні роликів відбувається переміщенні і нагрівання до розплавлення контактних поверхонь зварюваних виробів, які під дією стискаючих зусиль зварюються.
Поняття про газове зварювання, його переваги та недоліки. Для одержання зварного з'єднання при газовому зварюванні кромки основного металу і присадний метал нагрівають до розплавленого стану полум'ям горючих газів, стиснених при допомозі спеціальних зварювальних пальників у суміші з киснем. В якості горючого газу найбільше застосування одержав ацетилен, який при згорянні в кисні дає температуру полум'я, достатню для зварювання сталей та більшості інших металів і сплавів. Для зварювання металів з температурою плавлення меншою, ніж у сталі. Можуть бути використані водень, природний газ і ін.
Газове зварювання застосовують при виготовленні листових і трубчастих конструкцій із маловуглецевих та низьколегованих сталей, для виправлення дефектів у відливках сірого чавуну та бронзи тощо.
Газове зварювання має переваги у мобільності, меншій експлуатаційній небезпечності та меншому впливу на здорові людини (особливо на зір).
Технологія газового зварювання і різання металів.Основу технологіїгазового зварювання складає вид і склад ацетиленокисневого полум'я, спосіб та вибір режимів зварювання.
В більшості випадків при газовому зварюванні застосовують нормальне ацетиленокисневе полум'я, при якому на одну об'ємну частину ацетилену (Н2С2) припадає на 10...20 % більше кисню. Режим газового зварювання визначається вибраним діаметром присадного металу і потужністю газозварювального полум'я.
Газове різання здійснюють використовуючи горючі гази, зокрема ацетилен, який одержують із карбіду кальцію (СаС2) при його взаємодії з водою. Газове різання у струмені кисню використовують для різання сталі з вмістом вуглецю до 0,7 % та деяких низьколегованих сталей. Найвища температура полум'я у струмені ацетилену 3200 оС.
Плазмове різання металів являється найбільш продуктивним видом термічного різання, широко застосовується в машинобудуванні, в суднобудуванні, для різання листового металу значних габаритів тощо. Стиснення і стабілізація дуги здійснюється струменем газу разом із стовпом дуги, завдяки чому температура досягає 12000...20000 оС, і властивості металу при такому потужному спрямованому струменю теплової енергії практично не впливають на процес різання.
Нові види зварювання металів. До нових (нетрадиційних) способів зварювання можна віднести індукційне зварювання металу (нагрівання здійснюється індукційними струмами середньої і високої частоти з наступним його обтисненням), дифузійне (взаємна дифузія атомів у поверхневому шарі контактуючих матеріалів у вакуумі або атмосфері інертного газу), зварювання ультразвуком, холодне зварювання тиском (за рахунок значних зусиль стиснення), зварювання тертям (перетворення механічної енергії при взаємному переміщенні зварюваних поверхонь у теплову), плазмово-дугове, зварювання вибухом тощо.
Поняття про обробку металів різанням. Загальні основи процесу різання металів.Обробкою конструкційних матеріалів різанням називається процес відокремлення різальними інструментами шару матеріалу від заготовки для одержання необхідної форми деталі.
Для забезпечення встановленої точності розмірів, і шорсткості поверхні більшість деталей обробляються на верстатах зняттям стружки, тобто відбувається процес різання лезовими і абразивними інструментами.
Для одержання поверхні заданої форми і розмірів заготовки і інструменти закріплюються на металорізальних верстатах, робочі органи яких надають їм руху необхідної траєкторії із встановленою швидкістю і силою.
Рухи виконавчих органів верстатів поділяють на робочі і допоміжні. Робочими називають рухи, при яких із заготовки знімається стружка; допоміжними - рухи, при яких із заготовки стружка не знімається (підвід та відвід інструменту та ін.).
Робочий рух можна розкласти на головний рух і рух подачі. Головним називають рух, швидкість якого найбільша. Зняття стружки здійснюється в основному при поєднанні головного руху і руху подачі.
Фізичні явища, що відбуваються під час різання металів.Різання металів супроводжується складною сукупністю різних деформацій - зминання, зсуву, зрізу, що супроводжуються тертям відокремлюваної стружки об передню поверхню різця і тертям поверхні різання об задню поверхню різця. В результаті пружно-пластичної деформації металу, яка відбувається під впливом різального інструменту, утворюються нові поверхні.
Заготовці від шпинделя верстату передається головний обертальний рух, різцю супортом верстату надається рух подачі; обидва ці рухи здійснюються безперервно. То ж відбувається процес поверхневого різання.
Глибина різання t - відстань між оброблюваною і обробленою поверхнями, виміряна по перпендикуляру до осі заготовки, мм:
t = (d1-d2)/2.
Подача s - переміщення різця за один оберт заготовки, мм/хв.
Матеріали для курсових робіт
Енергетика
Електроенергію виробляють на електростанціях за рахунок використання енергії, схованої в різних природних ресур, це відбувається в основному на теплових (ТЕС) і атомних електростанціях (АЕС), працюючих по тепловому циклу.
Типи теплових електростанцій
За видом генерованої і відпускної енергії теплові електростанції поділяють на два основних типи: конденсаційні (КЕС), призначені тільки для виробництва електроенергії, і теплофікаційні, або теплоелектроцентралі (ТЕЦ). Конденсаційні електричні станції,що працюють на органічному паливі, будують поблизу місць його добування, а теплоелектроцентралі розміщують поблизу споживачів тепла - промислових підприємств і житлових масивів. ТЕЦ також працюють на органічному паливі, але на відміну від КЕС виробляють як електричну, так і теплову енергію у вигляді гарячої води і пари для виробничих і теплофікаційних цілей. До основних видів палива цих електростанцій відносяться: тверде - кам'яне вугілля, антрацит, напівантрацит, буре вугілля, торф, сланці; рідке - мазут і газоподібне - природний, коксовий, доменний і т.п. газ.
Атомні електростанції переважно конденсаційного типу використовують енергію ядерного палива.
Запорізька ТЕС (3600 МВт) - одна із найпотужніших ТЕС України (ділить 1-2-е місця з Вуглегірською ТЕС)
Частка загального виробітку по електростанціях, % АЕС
ТЕС на газі
ТЕС на мазуті
ТЕС на вугіллі та інших видах палива ГЕС і ЕС на інших,відновлювальних, видах палива
Встановлена потужність електростанцій в світі (всього), ГВт
У тому числі, % АЕС
ТЕС на газі
ТЕС на мазуті
ТЕС на вугіллі та інших видах палива ГЕС і ЕС на інших, відновлювальних, видах палива
У залежності від типу теплосилової установки для приводу електрогенератора електростанції поділяються на паротурбінні (ПТУ), газотурбінні (ГТУ), парогазові (ПГУ) і електростанції з двигунами внутрішнього згорання (ДЕС).
У залежності від тривалості роботи ТЕС впродовж року при покритті графіків енергетичних навантажень, які характеризуються числом годин використання встановленої потужності ?уст, електростанції прийнято класифікувати на: базові (τуст > 6000 год/рік); напівпікові (τуст = 2000-5000 год/рік); пікові (τуст < 2000 год/рік).
Базовими називають електростанції, які несуть максимально можливе постійне навантаження впродовж більшої частини року. У світовій енергетиці як базові використовують АЕС, високоекономічні КЕС, а також ТЕЦ при роботі по тепловому графіку.
Пікові навантаження покривають ГЕС, ГАЕС, ГТУ, що володіють маневреністю і мобільністю, тобто швидкими пуском і зупинкою. Пікові електростанції включаються в години, коли потрібно покрити пікову частину добового графіка електричного навантаження. Напівпікові електростанції при зменшенні загального електричного навантаження або переводяться на знижену потужність, або виводяться в резерв.
По технологічній структурі теплові електростанції поділяються на блочні й неблочні. При блочній схемі основне і допоміжне обладнання паротурбінної установки не мають технологічних зв'язків з обладнанням іншої установки електростанції. Для електростанцій на органічному паливі при цьому до кожної турбіни пара підводиться від одного або двох з'єднаних з нею котлів. При неблочній схемі ТЕС пара від всіх котлів надходить в загальну магістраль і звідти розподіляється по окремих турбінах.Вуглегірська ТЕС потужністю 3600 МВт
Південно-Українська АЕС потужністю 3000 МВт
На конденсаційних електростанціях, які входять у великі енергосистеми, застосовуються тільки блочні системи з проміжним перегрівом пари. Неблочні схеми з поперечними зв'язками по парі та воді застосовуються без проміжного перегріву.
Принцип роботи й основні енергетичні характеристики теплових електростанцій
Електроенергію на електростанціях виробляють за рахунок використання енергії, схованої в різних природних ресурсах (вугілля, мазут, уран та ін.), за достатньо простим принципом, реалізуючи технологію перетворення енергії. Загальна схема ТЕС (див. мал.1.1) відображає послідовність такого перетворення одних видів енергії в інші та використання робочого тіла (вода, пара) в циклі теплової електростанції. Паливо (в даному випадку вугілля) згоряє в котлі, нагріває воду і перетворює її в пару. Пара подається в турбіни, які перетворюють теплову енергію пари в механічну енергію і приводять в дію генератори, виробляючи електроенергію .
Сучасна теплова електростанція - це складне підприємство, яке включає велику кількість різноманітного обладнання. Склад обладнання електростанції залежить від вибраної теплової схеми, виду використовуваного палива і типу системи водопостачання.
Основне обладнання електростанції включає: котельні й турбінні агрегати з електричним генератором і конденсатором. Ці агрегати стандартизовані по потужності, параметрах пари, продуктивності, напрузі та силі струму і т.д. Тип і кількість основного обладнання теплової електростанції відповідають заданій потужності й передбаченому режиму її роботи. Існує і допоміжне обладнання, яке служить для відпуску теплоти споживачам і використання пари турбіни для підігріву живильної води котлів і забезпечення власних потреб електростанції. До нього відноситься обладнання систем паливопостачання, деаераційно-живильної установки, конденсаційної установки, теплофікаційної установки (для ТЕЦ), систем технічного водопостачання, маслопостачання, регенеративного підігріву живильної води, хімводопідготовки, розподілу і передачі електроенергії .
На всіх паротурбінних установках застосовується регенеративний підігрів живильної води, який суттєво підвищує теплову і загальну економічність електростанції, оскільки в схемах з регенеративним підігрівом потоки пари, що відводяться із турбіни в регенеративні підігрівачі, здійснюють роботу без втрат в холодному джерелі (конденсаторі). При цьому для одної і тої ж електричної потужності турбогенератора витрата пари в конденсаторі знижується і в результаті к.к.д. установки росте.
Тип застосовуваного парового котла (див. розділ 2) залежить від виду палива, яке використовується на електростанції. Для найбільш розповсюджених палив (копалини: вугілля, газ, мазут, фрезторф) застосовуються котли з П-, Т-подібною і баштовою компоновкою і топковою камерою, розробленою відповідно до того чи іншого виду палива. Для палив з легкоплавкою золою використовуються котли з рідким шлаковидаленням. При цьому досягається високе (до 90%) вловлювання золи в топці й знижується абразивне зношення поверхонь нагріву. Із цих же міркувань для високозольних палив, таких як сланці та відходи вуглезбагачення, застосовуються парові котли з чотирьохходовою компоновкою. На теплових електростанціях використовуються, як правило, котли барабанної або прямоточної конструкції.
Турбіни і електрогенератори узгоджуються по шкалі потужності. Кожній турбіні відповідає певний тип генератора. Для блочних теплових конденсаційних електростанцій потужність турбін відповідає потужності блоків, а число блоків визначається заданою потужністю електростанції. У сучасних блоках використовуються конденсаційні турбіни потужністю 150, 200, 300, 500, 800 і 1200 МВт з проміжним перегрівом пари.
На ТЕЦ застосовуються турбіни (див. підрозділ 4.2) з протитиском (типу Р), з конденсацією і виробничим відбором пари (типу П), з конденсацією і одним або двома теплофікаційними відборами (типу Т), а також з конденсацією,промисловим і теплофікаційними відборами (типу ПТ). Турбіни типу ПТ також можуть мати один або два теплофікаційних відбори. Вибір типу турбіни залежить від величини і співвідношення теплових навантажень. Якщо переважає опалювальне навантаження, то в додаток до турбін ПТ можуть бути встановлені турбіни типу Т з теплофікаційними відборами, а при перевазі промислового навантаження - турбіни типів ПР і Р з промисловим відбором і протитиском.
У даний час на ТЕЦ найбільше розповсюдження мають установки електричною потужністю 100 і 50 МВт, що працюють на початкових параметрах 12,7 МПа, 540-560°С. Для ТЕЦ великих міст створені установки електричною потужністю 175-185 МВт і 250 МВт (з турбіною Т-250-240). Установки з турбінами Т-250-240 є блочними і працюють при надкритичних початкових параметрах (23,5 МПа, 540/540°С).
Особливістю роботи електричних станцій в мережі є те, що загальна кількість електричної енергії, вироблюваної ними в кожний момент часу, повинна повністю відповідати споживаній енергії. Основна частина електричних станцій працює паралельно в об'єднаній енергетичній системі, покриваючи загальне електричне навантаження системи, а ТЕЦ одночасно і теплове навантаження свого району. Є електростанції місцевого значення, призначені для обслуговування району і не підключені до загальної енергосистеми.
Графічне зображення залежності електроспоживання в часі називають графіком електричного навантаження. Добові графіки електричного навантаження (мал. 1.5) змінюються в залежності від часу року, дня тижня і характеризуються зазвичай мінімальним навантаженням в нічний період і максимальним навантаженням в години пік (пікова частина графіка). Поряд із добовими графіками велике значення мають річні графіки електричного навантаження (мал. 1.6), які будуються за даними добових графіків.Мал. 1.6. Графік річного електричного навантаження за тривалістю: I - базове навантаження; II - проміжне навантаження; III - пікове навантаження
Графіки електричних навантажень використовуються при плануванні електричних навантажень електростанцій і систем, розподілі навантажень між окремими електростанціями і агрегатами, в розрахунках по вибору складу робочого і резервного обладнання, визначенні потрібної встановленої потужності і необхідного резерву, числа і одиничної потужності агрегатів, при розробці планів ремонту обладнання і визначенні ремонтного резерву та ін.
При роботі з повним навантаженням обладнання електростанції розвиває номінальну або максимально тривалу потужність (продуктивність), яка є основною паспортною характеристикою агрегату. На цій найбільшій потужності (продуктивності) агрегат повинен довго працювати при номінальних значеннях основних параметрів. Однією з основних характеристик електростанції є її встановлена потужність, яка визначається як сума номінальних потужностей всіх електрогенераторів і теплофікаційного обладнання з врахуванням резерву.
Робота електростанції характеризується також числом годин використання встановленої потужності, яке залежить від того, в якому режимі працює електростанція. Для електростанцій, які несуть базове навантаження, число годин використання встановленої потужності складає 6000-7500 год/рік, а для працюючих в режимі покриття пікових навантажень - менше 2000-3000 год/рік.
Навантаження, за якого агрегат працює з найбільшим к.к.д., називають економічним навантаженням. Номінальне тривале навантаження може дорівнювати економічному. Інколи можлива короткочасна робота обладнання з навантаженням на 10-20% вищим номінального при більш низькому к.к.д. Якщо обладнання електростанції стійко працює з розрахунковим навантаженням при номінальних значеннях основних параметрів або при зміні їх в допустимих межах, то такий режим називається стаціонарним.
Режими роботи з установленими навантаженнями, які відрізняються від розрахункових, або з неустановленими навантаженнями називають нестаціонарними або змінними режимами. При змінних режимах одні параметри залишаються незмінними і мають номінальні значення, інші - змінюються у визначених допустимих межах. Так, при частковому навантаженні блоку тиск і температура пари перед турбіною можуть залишатись номінальними, в той час як вакуум в конденсаторі й параметри пари у відборах змінюються пропорційно навантаженню. Можливі також нестаціонарні режими, коли змінюються всі основні параметри. Такі режими мають місце, наприклад, при пуску і зупинці обладнання, скиданні та накиді навантаження на турбогенераторі, при роботі на змінних параметрах і називаються нестаціонарними.Мал. 1.8. Сумарний річний графік теплового навантаження по тривалості: I - опалювальний період; II - літній період
Теплове навантаження електростанції використовується для технологічних процесів і промислових установок, для опалення і вентиляції виробничих, житлових і громадських будівель, кондиціювання повітря і побутових потреб. Для виробничих цілей зазвичай потрібна пара тиском від 0,15 до 1,6 МПа. Проте, щоб зменшити втрати при транспортуванні й уникнути необхідності безперервного дренування води із комунікацій, з електростанції пару відпускають дещо перегрітою. На опалення, вентиляцію і побутові потреби ТЕЦ подає зазвичай гарячу воду з температурою від 70 до 180°С.
Теплове навантаження, що визначається витратою тепла на виробничі процеси і побутові потреби (гаряче водопостачання), залежить від зовнішньої температури повітря. В умовах України влітку це навантаження (як і електричне) менше зимового. Промислове і побутове теплові навантаження змінюються впродовж діб, крім того, середньодобове теплове навантаження електростанції, що витрачається на побутові потреби, змінюється в робочі та вихідні дні.
Ефективність роботи ТЕС характеризується різними техніко-економічними показниками, одні з яких оцінюють досконалість теплових процесів (к.к.д., витрати теплоти і палива), а інші характеризують умови, в яких працює ТЕС.
Як видно із малюнків, комбінований виробіток електричної і теплової енергії забезпечує значне підвищення теплової економічності електростанцій завдяки зменшенню втрати теплоти в конденсаторах турбін.
Найбільш важливими і повними показниками роботи ТЕС є собівартості електроенергії і теплоти.
Теплові електростанції мають як переваги, так і недоліки в порівнянні з іншими типами електростанцій. Можна вказати наступні переваги ТЕС:
• відносно вільне територіальне розміщення, пов'язане з широким розповсюдженням паливних ресурсів;
• здатність (на відміну від ГЕС) виробляти енергію без сезонних коливань потужності;
• території відчуження і виведені із господарського обороту землі під спорудження і експлуатацію ТЕС, як правило, значно менші, ніж це необхідно для АЕС і ГЕС;
• ТЕС споруджуються значно швидше, ніж ГЕС або АЕС, а їх питома вартість на одиницю установленої потужності нижча в порівнянні з АЕС.
У той же час ТЕС володіють великими недоліками:
• для експлуатації ТЕС зазвичай потрібно набагато більше персоналу, ніж для ГЕС, що пов'язано з обслуговуванням досить масштабного за об'ємом паливного циклу;
• робота ТЕС залежить від поставок паливних ресурсів (вугілля, мазут, газ, торф, горючі сланці);
• змінність режимів роботи ТЕС знижує ефективність, підвищує витрату палива і призводить до підвищеного зношення обладнання;
• існуючі ТЕС характеризуються відносно низьким к.к.д. (в основному до 40%);
• ТЕС чинять прямий і неблагополучний вплив на навколишнє середовище і не є екологічно «чистими» джерелами електроенергії.
Найбільшу шкоду екології навколишніх регіонів завдають електростанції, які працюють на вугіллі, особливо високозольному. Серед ТЕС найбільш «чистими» є станції, що використовують в своєму технологічному процесі природний газ.
За оцінками експертів, ТЕС всього світу викидають в атмосферу щорічно близько 200-250 млн. тонн золи, більше 60 млн. тонн сульфідного ангідриду, велику кількість оксидів азоту і вуглекислого газу (який викликає так званий парниковий ефект і призводить до довготермінових глобальних кліматичних змін), поглинаючи велику кількість кисню. Крім того, на даний час встановлено, що надлишковий радіаційний фон навколо теплових електростанцій, які працюють на вугіллі, в середньому у світі в 100 разів вищий, ніж поблизу АЕС такої ж потужності (вугілля в якості мікродомішок майже завжди містить уран, торій і радіоактивний ізотоп вуглецю). Тим не менше, добре відпрацьовані технології будівництва, обладнання і експлуатації ТЕС, а також менша вартість їх спорудження приводять до того, що на ТЕС припадає основна частина світового виробництва електроенергії. З цієї причини удосконаленню технологій ТЕС і зниженню негативного впливу їх на навколишнє середовище у всьому світі приділяється велика увага .
Загальні відомості про відновлювальні нетрадиційні джерела енергії
Сучасна енергетика в основному базується на невідновлювальних джерелах енергії, які, маючи обмежені запаси, є вичерпними і не можуть гарантувати стійкий розвиток світової енергетики на тривалу перспективу, а їх використання - один з головних факторів, який призводить до погіршення стану навколишнього середовища і його кризового стану.
До нетрадиційних (альтернативних) відносяться відновлювальні джерела енергії (ВДЕ), які використовують потоки енергії Сонця, енергію вітру, теплоти Землі, біомаси, морів і океанів, річок, існуючих постійно або періодично в навколишньому середовищі й у майбутній перспективі практично невичерпані. Всі ВДЕ поділяються на дві групи, що використовують пряму енергію сонячного випромінювання і її вторинні прояви (побічна сонячна енергія), а також енергію взаємодії Сонця, Місяця і Землі.
Результатом побічної діяльності Сонця є відповідні ефекти в атмосфері, гідросфері та геосфері у вигляді вітру, гідроенергії, енергії течій, хвиль, припливної енергії, теплової енергії навколишнього середовища тощо .
До нетрадиційних відновлювальних джерел енергії відноситься мала гідроенергетика з ГЕС потужністю до 30 МВт, а в ряді країн до 10 МВт.
Основними перевагами ВДЕ в порівнянні з традиційними невідновлювальними джерелами є:
• практично невичерпні ресурси;
• зниження негативного впливу на довкілля, включаючи викиди різних забруднюючих речовин, парникових газів, радіоактивне і теплове забруднення тощо.
Основними факторами, що обмежують використання нетрадиційних ВДЕ, є:
• мала густина енергетичного потоку, яка складає, наприклад, для сонячної енергії на поверхні Землі 1,36·10-3 МВт/м2, вітрової при швидкості вітру 10 м/с - 6·10-4 МВт/м2, геотермальної - 3·10-8 МВт/м2, в той час як для енергії АЕС - 0,2 МВт/м2;
• значна нерівномірність вироблення енергії в часі та її використання;
• відносно висока капіталоємність енергетичних установок і вартість виробленої електроенергії.
Необхідність широкого використання ВДЕ визначається швидким зростанням потреби в електричній енергії, яка за прогнозами має збільшитися у 2 рази до 2030 р. і в 4 рази до 2050 р. у порівнянні з 2000 р.; вичерпанням у видимому майбутньому розвіданих запасів органічного палива; кризовим станом довкілля в зв'язку із забрудненням оксидами азоту і сірки, вуглекислим газом, пилоподібними частинками від згорання палива, радіоактивним і тепловим забрудненням тощо.
Відновлювальні джерела енергії мають принципові відмінності, тому їх ефективне використання стає можливим на основі науково розроблених принципів перетворення ВДЕ у види, необхідні споживачам. У навколишньому середовищі завжди існують потоки відновлювальної енергії, тому в процесі розвитку відновлювальної енергетики необхідно орієнтуватись на місцеві енергоресурси, вибираючи з них найефективніші. Використання ВДЕ має бути багатоваріантним й комплексним, що дозволяє прискорити економічний розвиток регіонів. Наприклад, хорошою базою для використання ВДЕ можуть бути агропромислові комплекси, де відходи тваринництва й рослиноводства є сировиною для одержання біогазу, а також рідкого й твердого палива, виробництва добрив.
Відновлювальні енергоресурси
* Гідроенергоресурси водотоків наведені для великої і малої гідроенергетики.
Для ефективного планування енергетики на відновлювальних енергоресурсах необхідно: по-перше, систематичне дослідження навколишнього середовища, аналогічне дослідженням геологічного характеру при пошуку нафти або газу, по-друге, вивчення потреб конкретного регіону в енергії для промислового, сільськогосподарського виробництва й побутових потреб. Зокрема, щоб вибрати найекономічніше джерело енергії, необхідно знати структуру споживачів енергії.
Однією з найважливіших характеристик відновлювальних джерел енергії є їх енергетичний потенціал - показник, який визначає кількість енергії, властиву відповідному виду ВДЕ.
Для оцінки енергетичних ресурсів відновлювальних джерел енергії, можливих для використання, розрізняють наступні види енергетичного потенціалу ВДЕ:
• теоретичний, що характеризує загальну кількість енергії;
• технічний - частина теоретичного потенціалу, яку принципово можливо використати за допомогою сучасних пристроїв;
• економічно ефективний - частина технічного потенціалу, яку в теперішній час доцільно використовувати, виходячи з економічних, соціальних, екологічних та інших факторів.
Сонячна енергетика
Густина сонячного потоку в космосі на межі земної атмосфери складає 1,36 кВт/м2, його максимальна інтенсивність на поверхні Землі - 1 кВт/м2 (при тривалості до 2 годин у літні дні), а його середня інтенсивність у більшості країн - 0,20-0,25 кВт/м2. Низька ступінь концентрації є недоліком при використанні сонячної енергії. Із загальної кількості сонячного випромінювання, що потрапляє на земну поверхню, 46% - розсіяна сонячна радіація, 54% - пряма сонячна радіація.У сонячній енергетиці, що широко розвивається, можна виділити два основних напрями: сонячна теплоенергетика, яка використовує сонячну енергію для отримання теплоти, і сонячна електроенергетика, котра використовує сонячну енергію для вироблення електроенергії.
При взаємодії сонячного випромінювання з природними процесами утворюються вторинні джерела енергії.